We’ve seen several instances where mass-produced gaming systems, such as the Microsoft Kinect Xbox 360 scanner, have been used for purposes other than gaming. Recently, a team of researchers from the Technical University of Denmark (DTU) published a paper, “Micro and nanoscale 3D printing using optical pickup unit from a gaming console,” on how they hacked a Microsoft Xbox 360 and used one of its common components to replace the costly, conventional optics in their research equipment and create their own, affordable 3D printer that can print objects at the micro and nanoscale. This is a great example of how access to microscale and nanoscale 3D printing can be made easier just by lowering the cost.
“With our 3D printer that can print micro and nanoscale 3D objects, we are able to go from tens of micrometers in printing resolution down to hundreds of nanometers without expensive specialized components,” explained PhD student Tien-Jen Chang. “And we also end up with a simpler and more compact nanoscale 3D printer compared to other stereolithography systems.”
Photograph of HD DVD’s OPU from (a) top view and (b) bottom view (purple and red arrows indicate the optical path of 405 nm and 650/780 nm laser, respectively). (c) Intrinsic optical module, sensors, and actuators. 1: 405 nm laser diode; 2: 650/780 nm laser diode; 3: diffraction grating; 4: dichroic cube beam splitter; 5: beam splitter; 6: fold mirror; 7: collimating lens; 8: objective lens; 9: protective layer; 10: CD/DVD/HD-DVD disc data layer; 11: coil; 12: magnet; 13: expanding lens; and 14: photodiode integrated circuit (PDIC). Purple line represents 405 nm laser, while the red line represents 650/780 nm laser. Dot-dashed line indicates the transformation of view direction between XY panel and XZ panel.
The team developed a stereolithography 3D printer, typically referred to as SLA or SL, though it’s called STL in the research paper; this technology uses light to cause chemical monomers and oligomers to cross-link together to form solid objects.
“In this paper, we present the application of an OPU (Fig. 1a–c) as a compact and cost-effective solution to replace the conventional STL optical system and to eliminate the complexity of a STL system dramatically,” they wrote.
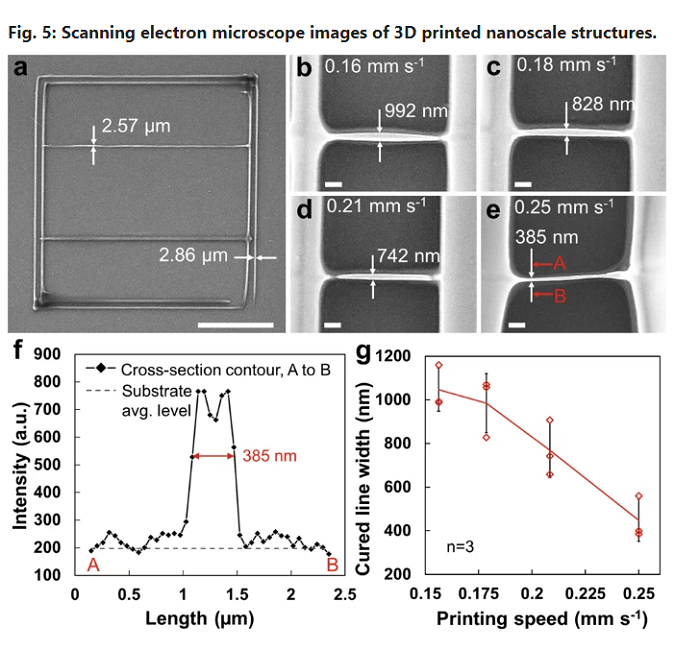
(a) 300 × 300 µm square printed with microscale lines with an approximate width of 3 µm. The nanoscale structures were cured at printing speeds of (b) 0.16, (c) 0.18, (d) 0.21, and (e) 0.25 mm s−1, resulting in line widths of 992, 879, 769, and 385 nm, respectively. Two vertical lines (width approximately 5 µm) were printed with a distance of 15 µm to suspend the nanometer structures. (f) Cross-section contour of 385-nm-width structure in e. (g) Cured nanoscale width according to printing speed at a laser power of 2.40 µW and a photopolymer thickness of 6 µm.
The researchers believe that the results from their nanoscale 3D printer could be useful for several different applications in the healthcare field.
“We believe that this technology can impact different areas of health technology. The original goal for developing our own 3D printer was to be able to print cubic centimeter volume with micro/nanoscale resolution for our micro-container based drug delivery development. And we couldn’t find a 3D printer system on the market that could do this. So we had to make our own,” Associate Professor En Te Hwu said.
“In addition to printing our microscale containers with a diameter of a human hair (100~300 micrometer) for more efficient oral drug delivery developments, this system can also be used to print painless microscale needles to be used on skin patches to speed up transdermal drug delivery developments. Another possibility is to use it for printing 3D structures for cell culture environment for more accurate ex-vivo drug testing studies. And a final example is to print biocompatible micro-devices with nanostructured surfaces that kill bacteria.”
Powered by Aniwaa
It’s not easy to make nanoscale photopolymerization a cost-effective solution. The use of the optical drive pickup unit, or OPU, from the Xbox is a good way to achieve this. The researchers explained that the OPU is used for reading and writing data from optical storage discs, including compact discs (CDs), DVDs, and Blu-rays.
“The mass produced OPU (costs less than five USD) provides not only a light source but also diffraction-limited optics in a compact size, similar to a car key,” the team wrote. “Given its high-precision measurements and multiple wavelength laser modes, the OPU has been used for various other applications, such as atomic force microscopy26,27,28, biosensing29,30, and photolithography31.”
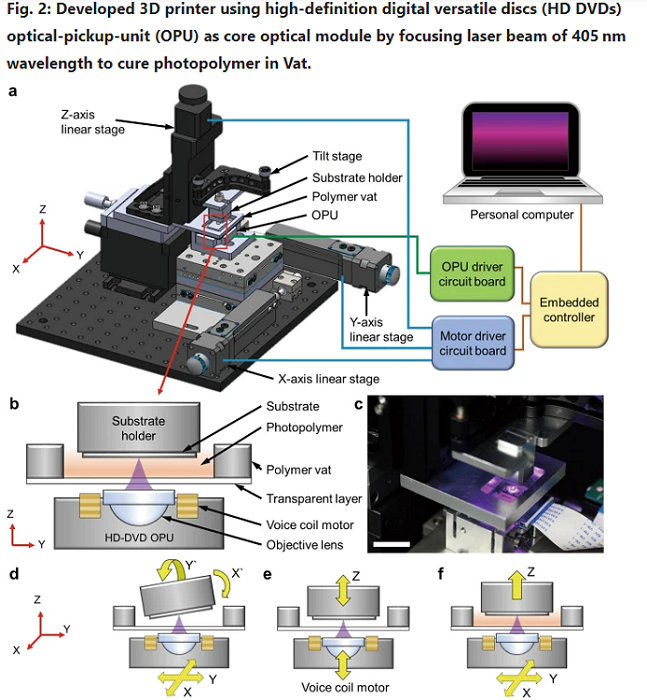
(a) Mechanism of printer with inverted stereolithography design and control system diagram. (b) Diagram of optical path. (c) Photograph of system during printing. (d) Substrate tilting diagram (X′ and Y′ represent tilting substrate along X-axis and Y-axis, respectively). (e) Vertical position initialization and objective lens translation diagrams. (f) Printing solid structures layer-by-layer process diagram.
They explained that a compact HD-DVD OPU can possibly simplify the design of a optical system, as it has “a finely adjustable diode laser” that allows the user to adjust the resolution from tens of micrometers all the way down to hundred of nanometers, without using expensive femtosecond lasers or oxygen radical scavenging. It also features “an optical working distance of 1.25 mm, which is four times that of a Blu-ray OPU,” making it a flexible option for SLA printing, and “equips multiple-wavelength (405/650/780 nm) continuous wave semiconductor laser diodes to read HD-DVD/DVD/CD data.”
The researchers used a commercial photopolymer to evaluate the performance of their nanoscale 3D printer with different laser exposure parameters, and also showed how its “substantially simplified optics” were used to 3D print stereoscopic microstructures. They were able to achieve a 385 nm resolution along the lateral direction, and the “XYZ nano-resolution linear stages enable a printing volume of up to 50 × 50 × 25 mm3.”

Fig. 6: Scanning electron microscope images of 3D printed structures. (a) Pyramid with height of approximately 850 µm and height of 25 µm per layer. (b) Tilted square tower. (c) Twisted tower. (d) Cylinder. (e) Gate-like structure.
Due to the fact that their printer uses much easier, less expensive optics, it could help set the stage for more affordable, high-resolution 3D printing on the micro and nanoscale. The team sees a lot of potential for commercialization, and plans to found a spin-off company in a few years.
Associate Professor En Te Hwu concluded, “In the end, our goal is to help patients experience better diagnostics and treatment, for example through more accurate medical diagnostics, more efficient oral drugs, and better skin patches.”
(Source: DTU Health Tech)
Be the first to comment